It’s not easy to teach old dogs new tricks, but at 135-year-old construction company Ballast Nedam, they were willing students. The Netherlands-based company has been making a transition over the past…
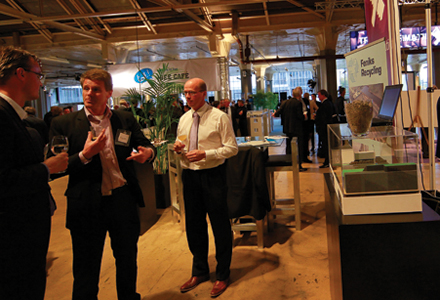
© 2025 Access Intelligence, LLC – All Rights Reserved. |